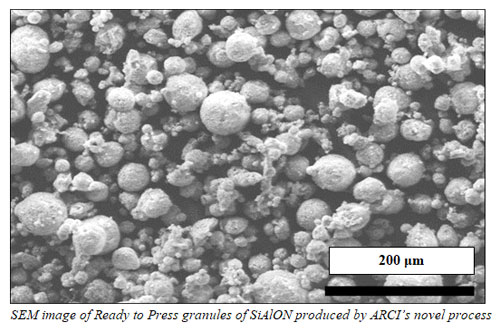
The new route for granule production which has been published in the journal of Advanced Powder Technology will help indigenous production of granulate nitride-based ceramic powders thus improving properties of a compacted part. The granules obtained with the help of this route are comparable with the commercially available granules.
Lack of reliability of ceramic products limits its application, especially in ones that are mobile in nature. Eliminating defects can help improve reliability. During compaction of ceramic powder, the uniformity in die (a metallic tool required for compacting ceramic/metal powder) filling through improved flowability is essential to ensure the defect-free products. Generally, the flowability of fine ceramic powder is an issue due to their irregular morphology based on the synthesis route and restricts flowability due to interparticle friction. An intermediate step of engineering morphology into spherical form to produce ready-to-press (RTP) granules prior to compaction is very important to improve the flowability.
The ARCI group formulated Aluminium nitride (AlN) based RTP granules along with silicon nitride (Si3N4), aluminium oxide (Al2O3), boron nitride (BN) and yttrium oxide (Y2O3) for in-situ formation of SiAlON while sintering of compacted parts at temperatures more than 1800oC. SiAlON is an excellent structural non-oxide ceramic having application potential in various vital sectors because of its unique combination of high Young’s modulus, moderate hardness, high fracture toughness, moderate thermal properties, excellent thermal shock resistance, excellent oxidation and corrosion resistance.
In view of the cumbersome process of using water-resistant (WR) coating on sensitive AlN and further the poor stability of such formulation with time, the facile route developed by ARCI offers an easy, simple alternative. The facile process to produce such granules comprises of dispersing the powders in suitable organic medium with a binder which promotes the dispersion in combination with imparting the strength to the granule in order to retain the spherical shape. The slurry with acceptable stability and also flow properties were sprayed into a chamber through an indigenously designed two-fluid nozzle. The size range of the granules were optimised with spherical morphology suitable for achieving flowability while compaction.
These RTP formulations were further subjected to Cold Isostatic pressing to produce cutting tools and crucibles for molten metal in foundries which on sintering at elevated temperature resulted in the in-situ formation of SiAlON ceramics.
Currently, the granulation process is established on a laboratory scale, and techno-commercial analysis will be undertaken for technology development. The process can help improve the reliability of nitride-based ceramic products shaped through compaction process and enhance the indigenous manufacturing capability of nitride-based ceramics in the country.
Publication links:
(1) A facile route for producing spherical granules comprising water-reactive aluminium nitride added composite powders, published in “Advanced Powder Technology” (In Press, available online), DOI: https://doi.org/10.1016/j.apt.2020.03.009.
(1) A facile route for producing spherical granules comprising water-reactive aluminium nitride added composite powders, published in “Advanced Powder Technology” (In Press, available online), DOI: https://doi.org/10.1016/j.apt.2020.03.009.
(2) Effect of porosity on the structure and properties of β-SiAlON ceramic, published in “Journal of Alloys and Compounds”, 779 (2019), 590-598.
(3) Load dependent indentation behavior of β-SiAlON and α-Silicon Carbide, “Journal of Advanced Ceramics”, 2(2) (2013), 185-192.
For further details, Dr. Prasenjit Barick (prasenjit[at]arci[dot]res[dot]in) can be contacted.